Sustainable platooning project helps with potential savings in the areas of CO2 emissions and fuel consumption
The “Aeroptimizer” platooning project calculates the ideal platoon arrangement for greater efficiency and higher savings potential in the areas of CO2 emissions and fuel consumption. In addition, the drive-independent calculation model enables fair, savings and responsibility-dependent charging models to be derived.
With the “Aeroptimizer” we are developing an evaluation method for determining the optimal arrangement of different vehicles in mixed platoons together with Hödlmayr International, the Linz Center of Mechatronics and the Logistikum – logistics department of the University of Applied Sciences Upper Austria. In this way, CO2 emissions can be reduced and a fuel reduction of 4 to 5 percent can be achieved.
However, in platooning not every truck is arranged in an aerodynamically sensible way and not every participant in the platoon benefits to the same extent. Therefore, this new evaluation method is the key to calculate savings potentials under realistic conditions with different vehicle types.
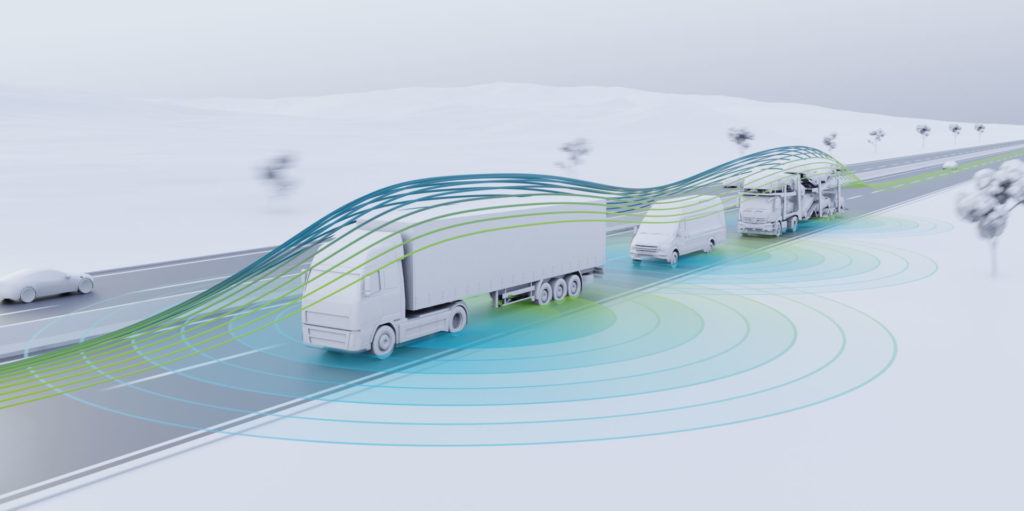
What makes platooning with „Aeroptimizer“ sustainable?
Autonomous vehicle technologies offer the opportunity to use our existing infrastructure much better in the future and to make road traffic more ecological and economical. Using the example of platooning, autonomous trucks can travel one behind the other at around ¼ of the previously prescribed distance. The resulting slipstream effects can save around 50% of the air resistance, which leads to 4-5% emission savings. Trucks driving in platoons also consume significantly less space on our motorways and the progressive surface sealing can be counteracted.
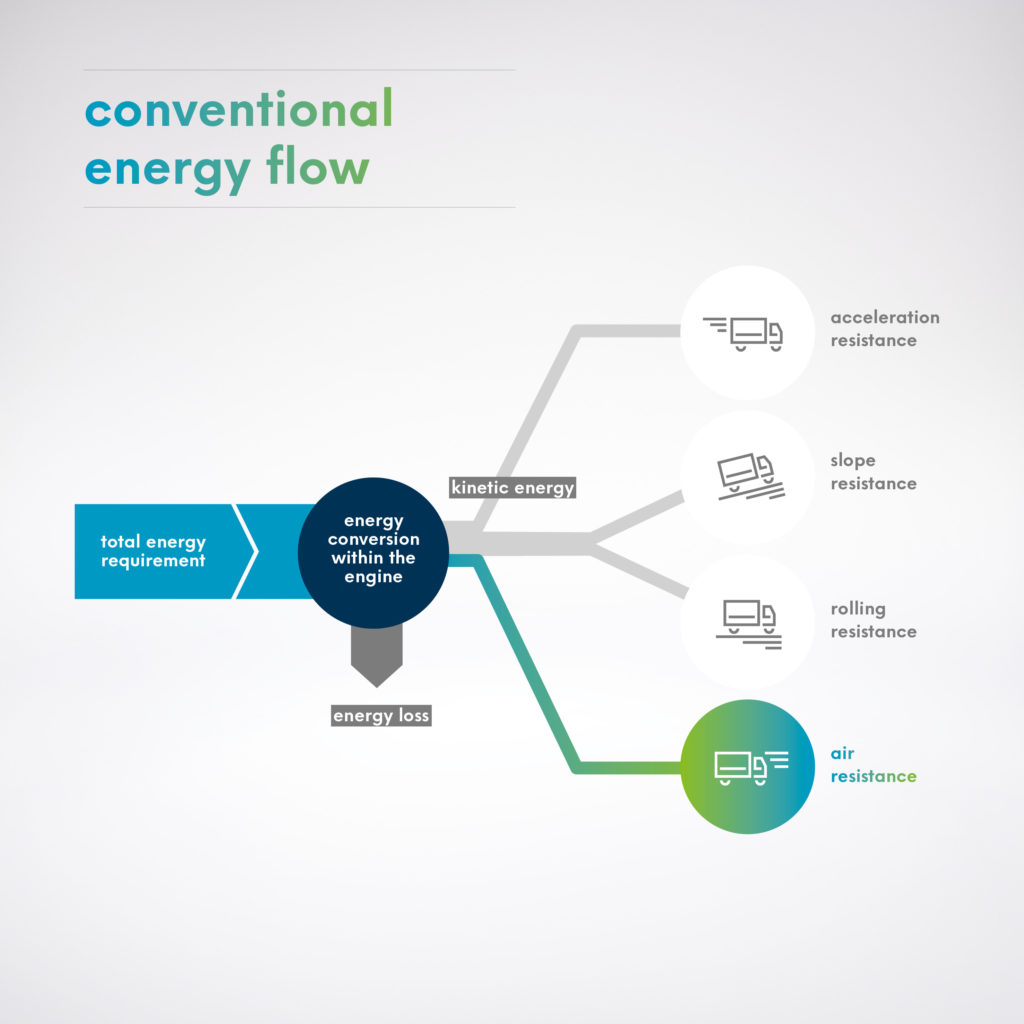
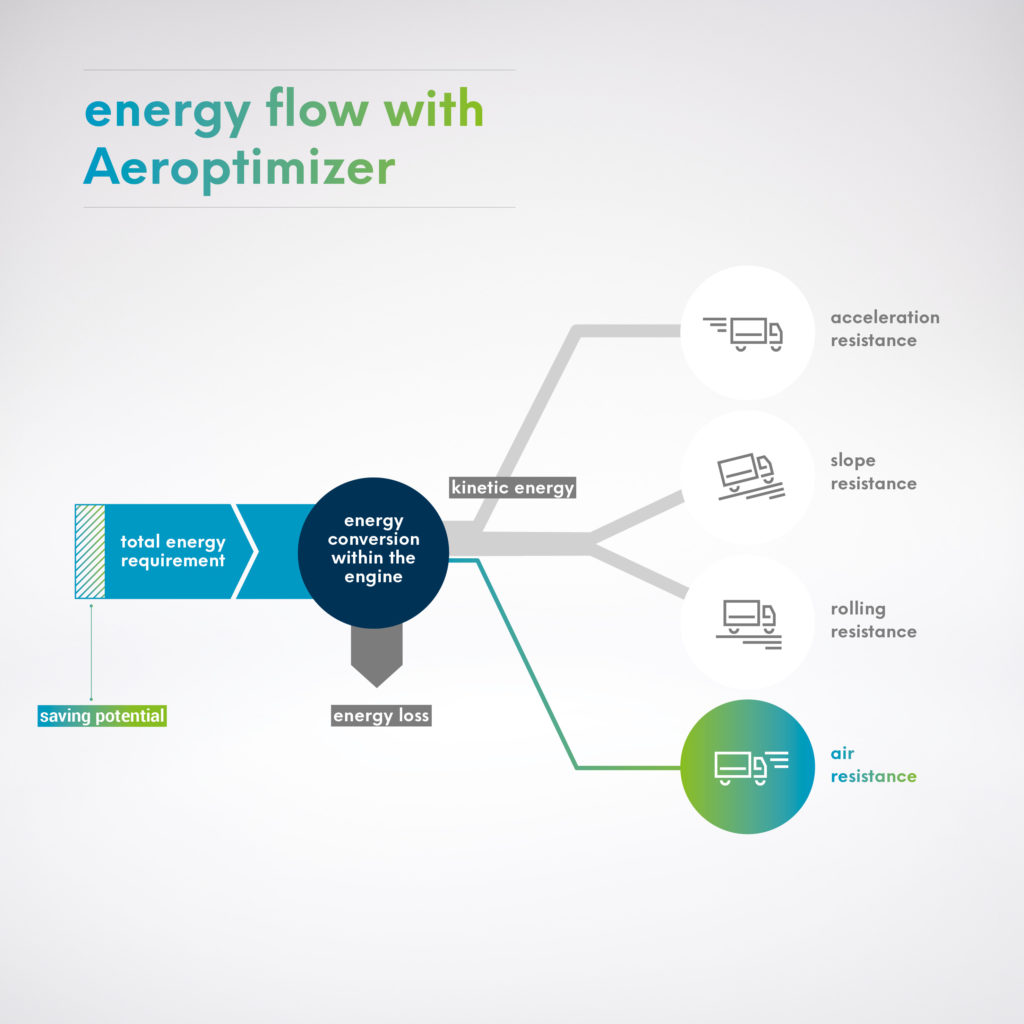
This is what makes the „Aeroptimizer“ in combination
with platooning so valuable for logisticians:
- The air resistance can be reduced by almost 50% through the optimized arrangement of the platooning vehicles
- Platooning achieves a CO2 reduction and a 4-5% reduction in fuel consumption
- The type of drive of the vehicle has no influence on the evaluation method
- With „Aeroptimizer“ fair, savings and responsibility-dependent billing models can be derived
The next steps towards sustainable platooning with „Aeroptimizer“
A CFD simulator (Computational Fluid Dynamics) has recently been built, with which the fluid mechanics of mixed platoons of articulated and vehicle transporters can be examined in different positions and at different distances. With the „Aeroptimizer“ the ideal position of each vehicle within the platoon can be calculated in order to achieve the greatest possible benefit for everyone. For the first time in platooning, the different sizes and shapes of vehicles are taken into account. From the composition of the ideal platoon, fair, savings and responsibility-dependent billing models can then be derived. In the second project phase, the „Aeroptimizer“ will be validated and calibrated using real measurements.
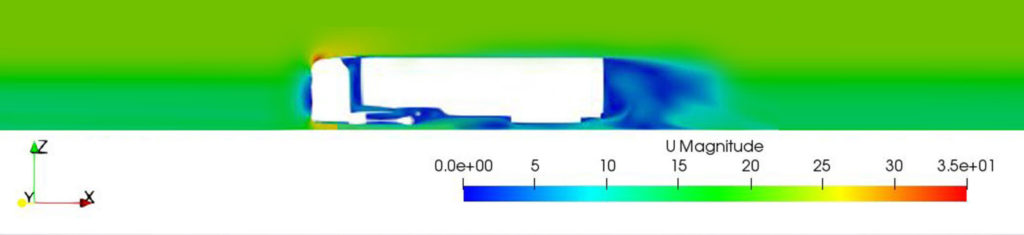
In a standard truck, the front and rear of the vehicle generate most of the air resistance.
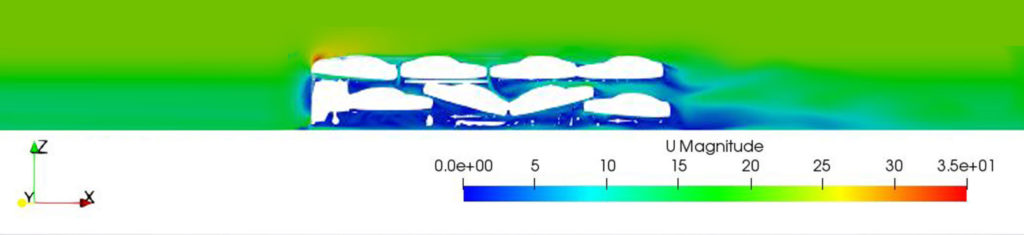
In a vehicle transporter, the front of the truck generates as much air resistance as a standard truck. The flow through the vehicle transporter with the individual vehicles generates a total of approx. 30% more air resistance than a standard truck.
Key messages slipstream effect:
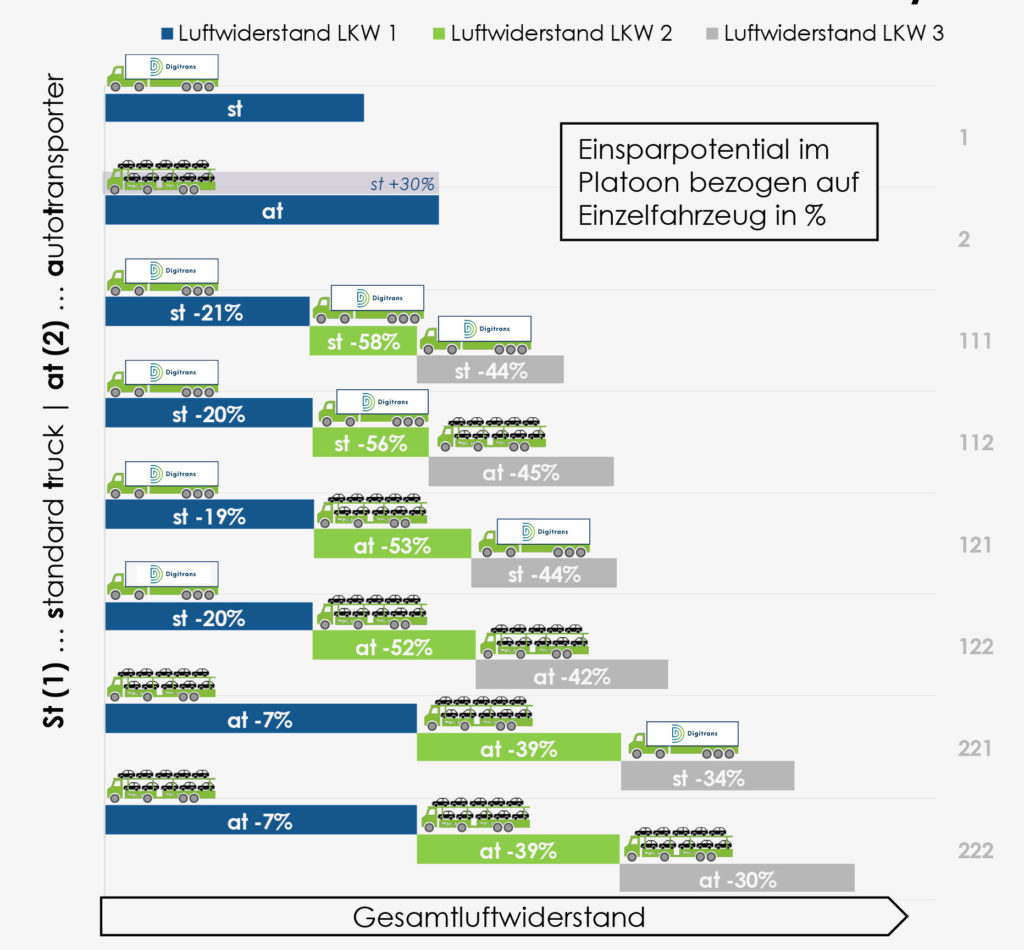
Core statements slipstream effect: Platoon distance 0.3s / ~7m at 80 km/h
- First truck in Platoon has the biggest impact on overall Platoon savings
- Standard truck Platoon (1-1-1) is the most efficient
- Greatest savings potential when driving behind one or more standard trucks
- Vehicle transporters should not drive first in the Platoon (regardless of who drives behind them)
- Slipstream effects decrease with increasing distance, but are still present
You might also be interested in
Further Insights
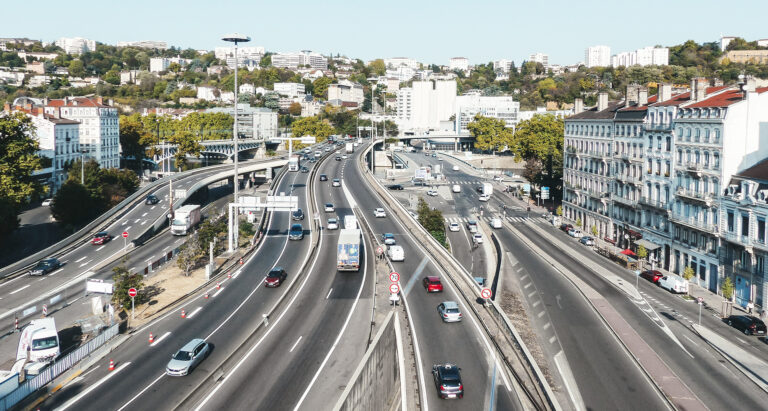
Cooperation with Logistikum FHOÖ – Foundation for safe, automated and networked freight transport in Upper Austria
The “Logistikum” of the FHOÖ is conducting research together with Digitrans on various research projects to further develop automated and networked freight transport. Currently, the focus is on the development of a real test field for automated driving in Upper Austria.
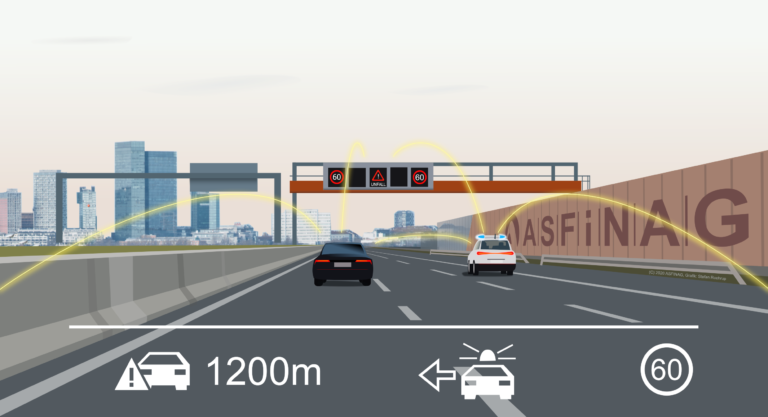
ASFINAG and Digitrans plan further steps towards automated driving in Upper Austria
With ASFINAG, Eva Tatschl-Unterberger, Managing Director of DigiTrans GmbH, has brought an important partner on board to push the development of a real test field for automated driving on highways in the Linz central region. The cooperation is intended to help create the basis for safe automated driving.
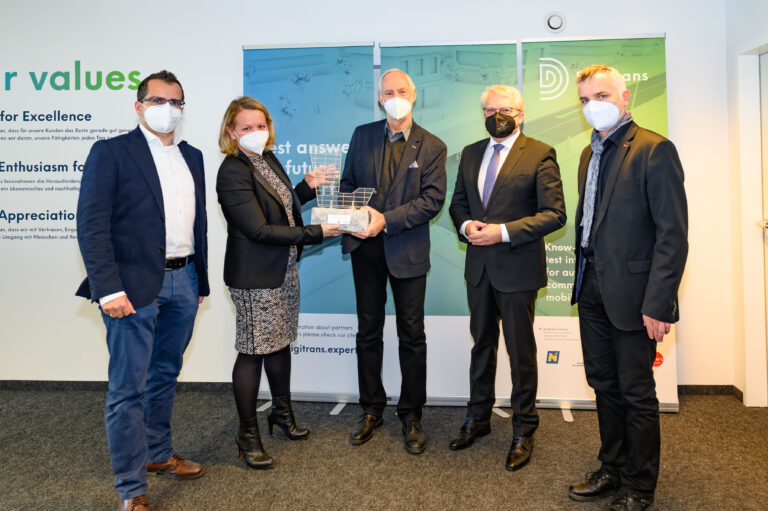
Digitrans selected as Linz Company of the Year 2021
Digitrans has been awarded as the Linz Company of the Year 2021 in the category of business cooperation. The award was presented personally by Linz Mayor Klaus Luger to CEO Eva Tatschl-Unterberger at the Digitrans Office in Linz